INŻYNIERIA MATERIAŁOWA 6/2017
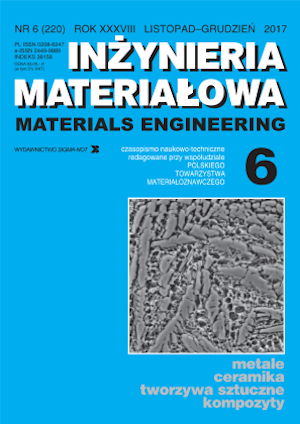
Adam Zych, Krzysztof Kulikowski, Beata Kucharska, Tadeusz Wierzchoń
Structure and adhesion of nickel-phosphorus coatings plated on the nitrided 1.2343 (WCL) steel
Struktura i przyczepność powłok niklowych do stali 1.2343 (WCL) po procesie azotowania jarzeniowego
DOI 10.15199/28.2017.6.1
Streszczenie
Celem badań było określenie wpływu struktury, twardości oraz rozwinięcia powierzchni warstwy azotowanej na stali 1.2343, a także procesu obróbki cieplnej powłoki Ni(P) na przyczepność powłoki niklowo-fosforowej do azotowanego podłoża. W pracy zawarto wyniki badań chropowatości powierzchni, mikrostruktury warstw kompozytowych, ich twardości oraz przyczepności
Abstract
Modern industry expects comprehensive solutions in terms of ensuring adequate exploitation properties of materials, such as high hardness, wear resistance, fatigue strength and corrosion resistance in aggressive environments. These requirements can be met via surface treatments, especially vigorously developed in recent years hybrid technologies, which merge various methods in the aspect of composite layers production. Those layers are characterized by complementing or entirely new properties in comparison to layers or coatings manufactured in separate processes. In this study the plasma nitriding process and electroless nickel plating are combined. In the production of composite layers consisting of surface layer and coating, in this particular case it is essential to ensure good adhesion of the Ni(P) coating to nitrided substrate. This paper presents microstructure (light microscopy), microhardness (crosssection and surface), surface roughness and scratch test results after different variants and steps of treatment of heat treated 1.2343 (WCL) steel. The study was conducted on the nitrided layers varying in structure and surface topography due to grinding prior to electroless nickel plating. The results show that heat treatment subsequent to electroless nickel plating leads to increase in composite layers’ hardness and adhesion of Ni(P) coating to nitrided layer. Moreover, Ni(P) coating might act as a solid lubricant in some cases.
Daria Mikołajczak, Michał Kulka, Natalia Makuch, Piotr Dziarski
Laser alloying of 316L steel with boron and Stellite-6
Laserowe stopowanie stali 316L borem i Stellite-6
DOI 10.15199/28.2017.6.2
Streszczenie
Stal 316L jest powszechnie stosowanym materiałem odpornym na korozję i żaroodpornym. Te korzystne właściwości zawdzięcza jednofazowej, austenitycznej mikrostrukturze i odpowiedniej zawartości węgla, chromu, niklu i molibdenu. To sprawia, że materiał ten jest stosowany często tam, gdzie jest spodziewane agresywne środowisko lub wysoka temperatura. Celem pracy było przeprowadzenie stopowania laserowego stali 316L z zastosowaniem materiału stopującego w postaci mieszaniny amorficznego boru i proszku Stellite-6. Bor amorficzny miał prowadzić do wytworzenia w strefie przetopionej twardych borków żelaza, chromu i niklu, podstawowych pierwiastków występujących w stali 316L. Dodatek kobaltu, głównego składnika proszku Stellite-6, miał powodować ograniczenie udziału borków w mikrostrukturze i sprzyjać jego odporności korozyjnej. Spodziewano się znacznego zwiększenia twardości oraz odporności na zużycie przez tarcie wytworzonej warstwy powierzchniowej w porównaniu ze stalą 316L nie poddaną żadnej obróbce.
Abstract
Austenitic 316L steel belongs to one of the most numerous groups of alloys with special properties. It is well-known for its most effective balance of carbon, chromium, nickel and molybdenum concentrations for corrosion resistance. However, under conditions of appreciable mechanical wear (adhesive or abrasive), this steel should be characterized by suitable wear protection. Diffusion boronizing and laser alloying with boron were often used in order to improve tribological properties of 316L steel. In this study, the method of laser alloying was modified in this way that alloying material contained the mixture of amorphous boron and Stellite-6 powders. The coated surface was remelted by the laser beam using TRUMPF TLF 2600 Turbo CO2 laser. After the laser alloying process, the composite surface layer was produced. Only two zones occurred in the laser-alloyed 316L steel: remelted zone and the substrate (base material). Heat-affected zone was invisible because the austenitic steel could not be hardened by typical heat treatment. The remelted zone consisted of hard ceramic phases (iron, chromium and nickel borides) in the soft austenitic matrix with the increased concentration of cobalt. Some properties of this layer were investigated and compared to the laser-alloyed layer with boron only. The produced layer was characterized by a compact microstructure which was free of cracks and gas pores. The layer was also uniform in respect of the thickness because of the high overlapping used during the laser treatment (86%). The obtained thickness was significantly higher than that obtained in case of diffusion boriding. In spite of the lower hardness of remelted zone, the increase in wear resistance of the proposed surface layer was observed in comparison with laser-alloyed 316L austenitic steel with boron only.
Aleksandra Pertek-Owsianna, Karolina Wiśniewska, Aneta Bartkowska
The influence of laser boronizing parameters on the mechanism of formation and properties of surface layers produced on iron alloys with various carbon content
Wpływ parametrów borowania laserowego na mechanizm tworzenia i właściwości warstw wierzchnich otrzymanych na stopach żelaza o zróżnicowanej zawartości węgla
DOI 10.15199/28.2017.6.3
Streszczenie
W pracy przeanalizowano mechanizm procesu borowania z użyciem lasera molekularnego TRUMPF TLF 2600 Turbo CO2. Bor wprowadzano przez przetopienie laserem pasty zawierającej bor z materiałem podłoża w postaci żelaza Armco oraz stali C45 i C90. Badania miały na celu określenie wpływu zawartości węgla w stopie żelaza oraz parametrów obróbki (moc lasera, prędkość posuwu wiązki, rodzaj i grubość warstwy pasty borującej) na mikrostrukturę, mikrotwardość oraz odporność na zużycie przez tarcie wytworzonej warstwy wierzchniej.
Abstract
This paper analyses the boronizing treatment which was performed by means of CO2 molecular laser with a power of 2600 W. Boron was introduced by remelting the paste with a thickness of 40÷120 mm, containing amorphous boron or iron-boron, use the material of the substrate, such as Armco iron or C45 and C90 types of steel. The influence of the boron paste thickness, variable P power from P = 0.78 kW to 1.82 kW, with the constant laser beam scanning velocity v = 2.88 m/min and material type on the mechanism of formation, microstructure, microhardness and frictional wear resistance of the formed layers (surface structure). After laser boronizing the surface layer consists of zone-structured tracks: melted zone, heat affected zone and the substrate. The melted zone contains boride-martensitic eutectic, in C45 and C90 types of steel there under the remelted zone there is a heat affected zone which is composed of a martensitic structure. With the increase in the laser power, width and depth of laser tracks increases in all the iron alloys with variable thickness of the applied amorphous boron paste. With the increase in the thickness of the boron paste, width of the laser tracks increases and depth of the laser tracks decreases with the constant beam power. The maximum dimensions of the remelted zone for C45 steel were: approx. 600 μm (width) and 350 μm (depth). The highest average microhardness of the surface layer reaches approx. 1500 HV0.1 and it decreases with the increase in power for all the iron alloys. Microhardness and frictional wear resistance of the layer boronized by means of laser with the use of the paste containing iron-boron is lower than that of the layer boronized with the use of the paste containing only boron.
Wojciech Napadłek, Wojciech Chrzanowski, Paweł Leoniuk
Fatigue contact durability of laser textured rolling bearings
Trwałość zmęczeniowa łożysk tocznych teksturowanych laserowo
DOI 10.15199/28.2017.6.4
Streszczenie
Celem badań trwałości zmęczeniowo-stykowej było określenie wpływu modyfikacji warstwy wierzchniej na walcowe łożyska toczne. Uwzględniając potrzeby badawcze wałeczkowych łożysk tocznych w warunkach modelowych z symulowanymi obciążeniami stałymi lub cyklicznie zmiennymi, opracowano w Wydziale Mechanicznym WAT koncepcję oraz projekt konstrukcyjny stanowiska do badań tribologiczno-zmęczeniowych w warunkach laboratoryjnych. W artykule przedstawiono koncepcję stanowiska do modelowych badań trwałości łożysk tocznych, a także wstępne wyniki badań trwałości zmęczeniowo-stykowej łożysk.
Abstract
Based on the pilot testing of cylindrical roller bearings, it might be concluded that the bearings quenched by volume and the secondary by laser show lower contact fatigue life in compare to bearings quenched only by volume (production conditions). One of the reason for this phenomenon might be of internal stresses in laser modified material surface layer due to the rapid non-equilibrium changes. The next stage of bearing research is secondary laser hardening tests after modification (optimization) of hardening parameters. Laser textured bearings in a variant in which lubricant reservoirs cover 25% of the inner raceway showed decreased stability in relation to the bearings after laser secondary hardening. Further laboratory tests will also identify the reason of accelerated degradation, i.e. pitting of laser textured bearings for variant in which lubricating reservoirs cover of 5% of the surface of the inner raceway which shows increased stability with respect to the bearing produced with standard manufacturing procedures in the range of 5÷10%. Due to the high differences of the obtained results of the bearing contact durability tests, further studies are still required.
Norbert Radek, Jacek Pietraszek, Agnieszka Szczotok
Laser treatment of heterogeneous surfaces formed by electro-spark deposition
Obróbka laserowa powierzchni niejednorodnych wytworzonych obróbką elektroiskrową
DOI 10.15199/28.2017.6.5
Streszczenie
Przez powierzchnie niejednorodne należy rozumieć powierzchnie mające wyodrębnione regularne obszary dające się opisać innymi niż pozostała część powierzchni właściwościami geometrycznymi, fizykomechanicznymi czy fizykochemicznymi. Obszary tworzące niejednorodność powierzchni powstają w wyniku użycia do ich wytworzenia innej technologii niż do pozostałej części powierzchni. Celem pracy było badanie wybranych właściwości powierzchni niejednorodnych wytworzonych za pomocą obróbki elektroiskrowej i laserowej. Uzyskane warstwy poddano następującym badaniom: analizie mikrostruktury, badaniom mikro- i makrogeometrii powierzchni oraz pomiarom mikrotwardości.
Abstract
This study is an investigation of the effect of laser treatment on the properties of surface coatings produced by a conventional electro-spark deposition (ESD) process. A combination of ESD process and laser treatment has been developed, and tested, and improvement of certain surface properties has been demonstrated. These coatings are heterogeneous surfaces, which mean that there are variable characteristics along the depth of the thin coating. The study is carried out on a conventional C45 steel as substrate, coated by Cu–Mo electrode by electro-spark deposition. The coating showed an improved metallurgical bond to the substrate material, and desirable surface topography, microstructure and micro-hardness distribution along the depth of the coating. The developed process has a minimal thermal effect on the bulk material, below the coating. This is combined with an exceptionally homogeneous hard outer surface. This combination demonstrated also improvements of certain tribological properties, such as a rise of seizure resistance of the rubbing surfaces. The properties of heterogeneous surfaces, based on laser treated ESD, are largely dependent upon material combination systems, manipulating methods, ESD and laser parameters as well as process control.
Sebastian Lipa, Radomir Atraszkiewicz, Leszek Klimek
Influence of a steel surface treatment on the wetting angle and free surface energy
Wpływ obróbki powierzchni stali na kąt zwilżania i swobodną energię powierzchniową
DOI 10.15199/28.2017.6.6
Streszczenie
Przez powierzchnie niejednorodne należy rozumieć powierzchnie mające wyodrębnione regularne obszary dające się opisać innymi niż pozostała część powierzchni właściwościami geometrycznymi, fizykomechanicznymi czy fizykochemicznymi. Obszary tworzące niejednorodność powierzchni powstają w wyniku użycia do ich wytworzenia innej technologii niż do pozostałej części powierzchni. Celem pracy było badanie wybranych właściwości powierzchni niejednorodnych wytworzonych za pomocą obróbki elektroiskrowej i laserowej. Uzyskane warstwy poddano następującym badaniom: analizie mikrostruktury, badaniom mikro- i makrogeometrii powierzchni oraz pomiarom mikrotwardości.
Abstract
This study is an investigation of the effect of laser treatment on the properties of surface coatings produced by a conventional electro-spark deposition (ESD) process. A combination of ESD process and laser treatment has been developed, and tested, and improvement of certain surface properties has been demonstrated. These coatings are heterogeneous surfaces, which mean that there are variable characteristics along the depth of the thin coating. The study is carried out on a conventional C45 steel as substrate, coated by Cu–Mo electrode by electro-spark deposition. The coating showed an improved metallurgical bond to the substrate material, and desirable surface topography, microstructure and micro-hardness distribution along the depth of the coating. The developed process has a minimal thermal effect on the bulk material, below the coating. This is combined with an exceptionally homogeneous hard outer surface. This combination demonstrated also improvements of certain tribological properties, such as a rise of seizure resistance of the rubbing surfaces. The properties of heterogeneous surfaces, based on laser treated ESD, are largely dependent upon material combination systems, manipulating methods, ESD and laser parameters as well as process control.
Monika Domarecka, Kinga Bociong, Michał Krasowski, Agata Szczesio, Jerzy Sokołowski
Influence of polymerization conditions on selected properties and the shrinkage stress generated during solidification of a nanohybrid universal restorative material
Wpływ warunków polimeryzacji na wybrane właściwości i naprężenia skurczowe generowane podczas naświetlania uniwersalnego materiału nanohybrydowego do wypełnień
DOI 10.15199/28.2017.6.7
Streszczenie
Cel pracy stanowiła analiza wpływu warunków prowadzenia polimeryzacji na wybrane właściwości uniwersalnego materiału nanohybrydowego do wypełnień.
Abstract
Curing processes of resin dental composites is connected with shrinkage stresses. It might influence the quality of dental restorations. Researchers make effort to reduce generated stresses. One of the methods is physical modification performed by changing the conditions of polymerization process. In this study the effect of the curing mode and the light intensity of selected curing lamps on the properties of Filtek Z550 was investigated. For this purpose, photoelastic studies were performed. Transparent and photoelastically sensitive plates made of epoxy resin were used in evaluation of contraction stress, that generates during photopolymerization of resin composites. The study also included microhardness and diametral tensile strength testing. The results show the relationship between cure method and reduction of generated shrinkage stresses. The concentration of stresses generated by material Filtek Z550 during photopolymerization were reduced significantly (in each case not less than 35%). The conventional cured samples had the highest value of DTS and HV1. There are no statistically significant differences between DTS and HV1 of the differently (method I–V) polymerized samples.
Dariusz FELCENLOBEN
Przesłanki odmowy wszczęcia administracyjnego postępowania w sprawie aktualizacji informacji zawartych w operacie ewidencji gruntów i budynków
DOI 10.15199/50.2018.1.1
Streszczenie
Celem artykułu jest przedstawienie zagadnienia prawnego, dotyczącego instytucji odmowy wszczęcia postępowania administracyjnego w sprawie aktualizacji informacji zawartych w operacie ewidencji gruntów i budynków. Odwołując się do obowiązujących norm prawa oraz poglądów judykatury, wykazano po zaistnieniu jakich przesłanek o charakterze podmiotowym i przedmiotowym organ prowadzący ewidencję gruntów i budynków zobligowany jest odmówić wszczęcia postępowania na wniosek osoby zainteresowanej lub je umorzyć w przypadku jego wcześniejszego wszczęcia.
Abstract
The aim of this article is to present a legal issue concerning the institution of refusing to initiate administrative procedure on updating information contained in the land and buildings register. Recalling the existing norms of law and the views of judicature, it was demonstrated that after the existence of certain conditions of subject and object nature, the authority keeping the land and buildings register is obliged to refuse initiation of the procedure at the request of the person concerned or to cancel it in case of its earlier initiation.
INŻYNIERIA MATERIAŁOWA 5/2017
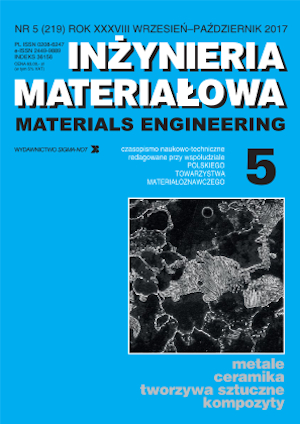
Marek Opiela
Development of microstructure and mechanical properties of forgings in the thermomechanical treatment
Kształtowanie struktury i właściwości mechanicznych odkuwek w procesie obróbki cieplno-plastycznej
DOI 10.15199/28.2017.5.1
Streszczenie
W pracy przedstawiono wyniki badań struktury i właściwości mechanicznych odkuwek ze stali z mikrododatkami Ti, Nb, V i B typu HSLA wytworzonej w kontrolowanym procesie obróbki cieplno- -plastycznej, poddanej następnie wysokiemu odpuszczaniu.
Abstract
The work presents research results of the influence of thermomechanical treatment via forging on microstructure and mechanical properties of newly elaborated microalloyed steel containing of 0.28% C, 1.41% Mn, 0.028% Ti, 0.027% Nb, 0.019% V and 0.003% B. The investigated steel is assigned to the production of forged elements for the automotive industry. Conditions of forging using the thermomechanical processing method were developed based on plastometric tests. Observations of the microstructures of thin foils were conducted using a TITAN80-300 FEI transmission electron microscope. The applied thermomechanical treatment allows to obtain a fine-grained microstructure of the austenite during hot-working and production of forged parts. These acquire advantageous mechanical properties and guaranteed crack resistance after controlled cooling from the end plastic deformation temperature and successive tempering. Forgings produced using the thermomechanical treatment method, consecutively subjected to tempering in a temperature range from 550 to 650°C, reveal values of YS0.2 which equal from 994 to 939 MPa, UTS from 1084 to 993 MPa, KV from 69 to 109 J, KV–40 from 55 to 83 J, and a hardness ranging from 360 to 310 HBW. The results obtained in this paper make it possible to develop an industrial technology of forgings with high mechanical properties and guaranteed crack resistance, and also at a decreased temperature, by using the thermomechanical treatment method.
Justyna Kasińska, Piotr Matusiewicz, Andrzej Czarski, Leopold Barwicki
Assessment of pearlite degradation in power industry cast steel after long-term exploitation
Ocena degradacji perlitu w staliwie dla energetyki po długotrwałej eksploatacji
DOI 10.15199/28.2017.5.2
Streszczenie
W wielu krajowych elektrowniach na elementy części ciśnieniowych kotłów, jak np. rury przegrzewaczy, są stosowane głównie normalizowane stale ferrytyczno-perlityczne. Po ich długotrwałej pracy zachodzi potrzeba oceny możliwości dalszej ich eksploatacji w warunkach pracy kotła lub turbiny. W stalach i staliwach o wyjściowej (przedeksploatacyjnej) mikrostrukturze ferrytyczno- -perlitycznej już po krótkich czasach eksploatacji w warunkach pełzania obserwuje się początkowe etapy pękania i fragmentacji płytek cementytu w perlicie. Kolejne etapy degradacji struktury to koagulacja wydzieleń, w tym cementytu w perlicie, wzrost wielkości niektórych rodzajów węglików, aż do utworzenia mikrostruktury ferrytycznej z bardzo zróżnicowaną morfologicznie fazą węglikową. Zastosowanie metod metalografii ilościowej do opisu mikrostruktury niewątpliwie rozszerza możliwości interpretacyjne obrazów mikrostruktury i ułatwia przeprowadzenie oceny stopnia ich degradacji zachodzącej w warunkach długotrwałej eksploatacji i pełzania. Obecnie nie istnieje znormalizowana/obliczeniowa ocena degradacji stali ferrytyczno-perlitycznych, a jedynie dokonuje się jej przez ocenę jakościową. Dlatego celem badań było wykorzystanie oraz ocena możliwości narzędzi metalograficznych do określenia stopnia degradacji perlitu w staliwie 25CrMo4 po długotrwałej eksploatacji.
Abstract
The paper presents the results of pearlite degradation analysis. The degradation level was evaluated on three specimens (cuttings) of low alloyed 20HM cast steel, sampled from various locations on the main body of the WP turbine exposed to creep (steam temperature 480°C, pressure 12.7 MPa). The mechanical properties (hardness, impact toughness) were performed. Microscopic observations were performed on nital-etched sections in the scanning electron microscope JSM 7100F. Microstructure analysis involved the characterization of microstructure morphology and quantitative metallography for describing pearlite degradation after a long-term exposure to creep. The measurements were performed using MetIlo image analysis program. There were measured the volume fraction of the regions with lamellar morphology, VV L and the pearlite degradation ratio, Lratio. In addition the microstructure class were determined on the basis of a qualitative assessment of changes in the morphology of pearlite regions.
Tomasz Mikuszewski, Agnieszka Tomaszewska, Grzegorz Moskal, Damian Migas, Dawid Niemiec
Characterization of primary microstructure of y-y' Co-Al-W cobalt-based superalloy
Charakterystyka mikrostruktury pierwotnej nadstopu kobaltu Co-Al-W typu y-y'
DOI 10.15199/28.2017.5.3
Streszczenie
Celem artykułu jest charakterystyka mikrostruktury pierwotnej stopu Co–9Al–9W w stanie bezpośrednio po odlaniu, z uwzględnieniem rozmieszczenia składników stopowych w rdzeniach dendrytów i obszarach międzydendrytycznych w różnych strefach odlewu oraz profilu mikrotwardości. Ważną kwestią była jednorodność rozmieszczenia wolframu w obszarach rdzeni dendrytów i w przestrzeniach międzydendrytycznych, co jest typowym problemem w stopach z dodatkiem wolframu.
Abstract
Present paper concerns primary structure of cobalt-based superalloys Co–9Al–9W with γ/γʹ structure, casted via induction melting process. Common problems described in literature, concerning difficulties in obtaining uniform distribution of tungsten, particularly in interdendritic areas were reason of utilization of modified casting process. Alter method is based on tungsten dosing into liquid metal bath of cobalt and aluminium during melting. This method allows to obtain microstructure characterized by considerably decreased microsegregation, especially in case of tungsten. This type of primary structure results in simplified and more economical homogenization performance of casts before further technological processes. Used method of casting give the possibility to obtain samples with small effect of segregations of alloying elements. Observed effect of interdendritic segregations were related to higher level of aluminium concentration and lower cobalt, but in both cases the measured difference was 2 to 4 % at.
Aleksandra Dubiel, Gabriela Górny, Marian Rączka, Ludosław Stobierski
The impact of TiN content on microstructure and mechanical properties of ceramic particulate composite Si3N4-TiN
Wpływ zawartości TiN na mikrostrukturę i właściwości mechaniczne ceramicznego kompozytu ziarnistego Si3N4-TiN
DOI 10.15199/28.2017.5.4
Streszczenie
W celu doskonalenia właściwości mechanicznych ceramiki z azotku krzemu tworzy się kompozyty ziarniste o osnowie z Si3N4, a jednym z takich materiałów jest kompozyt Si3N4-TiN. W kompozytach ziarnistych istotnymi zmiennymi mikrostrukturalnymi są m.in. udział objętościowy fazy rozproszonej, wielkość i kształt cząstek tej fazy oraz sposób ich rozmieszczenia w osnowie kompozytu. Celem pracy jest zbadanie wpływu udziału objętościowego fazy TiN oraz stopnia rozdrobnienia proszku TiN użytego do wytworzenia kompozytu Si3N4-TiN na jego mikrostrukturę oraz twardość, wytrzymałość na zginanie i odporność na kruche pękanie.
Abstract
The paper presents the results of study of the influence of the volume fraction of TiN phase on the microstructure and mechanical properties of the ceramic particulate composite Si3N4-TiN. Samples of the Si3N-TiN composite containing 5, 10, 15 or 20 vol. % of TiN phase were obtained by sintering mixtures of TiN and Si3N4 powders and sintering additives (6 wt % aluminium oxide and 4 wt % of yttrium oxide). Two types of TiN powder differing in the degree of fragmentation were used. Sintering was conducted at a pressure of 25 MPa at 1750°C for 1 hour. The resulting materials were subjected to quantitative analysis of the microstructure in order to determine the effect of TiN volume fraction and kind of TiN powder used on the microstructure of composites. Binary images showing the Si3N4 grains or TiN particles were obtained by the processing and binarization of SEM gray images of composite microstructure using the Aphelion computer software. The values of selected stereological parameters determining the size, shape and uniformity of distribution of the TiN particles and the size and shape of the matrix grains were determined. The study of the composite microstructure showed that for both types of TiN powders the increase of TiN volume fraction does not cause significant changes in size and shape of the Si3N4 grains. The increase in volume fraction of TiN phase produces the increase in the average TiN particle size in the composite, but cause only a slight change in their shape. Titanium nitride particles in the composite were smaller and somewhat more isometric and more uniformly distributed in the matrix when fine TiN powder was used. Measurements of flexural strength σf and fracture toughness KIc of all materials samples were conducted to determine the effect of composite microstructure changes on mechanical properties. The flexural strength and fracture toughness of the composites increase with the volume fraction of TiN phase. Composites with finer TiN particles are preferable from the point of view of better flexural strength, but higher values of fracture toughness are obtained for composites with coarser TiN particles.
Krzysztof Kulikowski, Adam Zych, Janusz Trojanowski, Jacek Rudnicki, Tadeusz Wierzchoń
Structure and properties of composite layers of nitrided layers with surface zone of manganese phosphate type produced on 32CDV13 steel
Struktura i właściwości warstw kompozytowych typu warstwa azotowana z powierzchniową strefą fosforanów manganu wytworzonych na stali 32CDV13
DOI 10.15199/28.2017.5.5
Streszczenie
Stal 32CDV13 (1.8522) ze względu na dobre właściwości mechaniczne jest materiałem stosowanym m.in. do produkcji wysokoobciążonych części maszyn i urządzeń. Zwiększenie trwałości i niezawodności wykonywanych elementów realizowane jest obecnie m.in. z zastosowaniem konwencjonalnych obróbek powierzchniowych, takich jak procesów nawęglania, nagniatania i hartowania powierzchniowego. Alternatywę dla tych rozwiązań stanowią procesy hybrydowe prowadzące do uzyskiwania warstw kompozytowych. Łączą one od dwóch do kilku technik obróbek powierzchniowych, umożliwiając wytworzenie warstw o unikatowych, wzajemnie uzupełniających się właściwościach. W ramach realizowanych badań w celu poprawy odporności na zużycie przez tarcie wytworzono na stali 32CDV13 w procesie hybrydowym łączącym proces azotowania jarzeniowego z fosforanowaniem chemicznym warstwy kompozytowe typu strefa dyfuzyjna azotu w sorbicie + strefa azotków żelaza ε + γʹ + powierzchniowa strefa fosforanów manganowych. Przeprowadzono badania struktury wytworzonych warstw oraz badania odporności na zużycie metodą „kula–tarcza”.
Abstract
Due to its high mechanical properties the 32CDV13 steel is widely used in the industry for the production of highly loaded parts of machines and equipment. The increase in the durability and the reliability of elements is currently being achieved by using conventional methods of surface treatments: carburizing processes, burnishing and surface hardening. Hybrid processes constitute an alternative to these solutions, leading to obtaining of composite layers. They combine two or more techniques during surface treatments, enabling the formation of surface layers with unique and complementary properties. This paper presents the structure (light microscopy, SEM) and the results of friction wear resistance (“ball on disc” method) of composite layers produced on heat treated 32CDV13 steel after it was (hardness 36 HRC) subjected to the hybrid process which combined the glow discharge nitriding process and phosphating method. The results show improvement of tribological properties, especially reduction of friction coefficient in comparison to nitrided layer.
Monika Madej, Dariusz Ozimina, Andrzej Krzyszkowski, Jacek Świderski, Krystian Milewski
The influence of the structure direction on diamond-like carbon coatings tribological properties
Wpływ ukierunkowania struktury powłok diametopodobnych na właściwości tribologiczne
DOI 10.15199/28.2017.5.6
Streszczenie
Powłoki diamentopobne DLC cieszą się coraz większym zainteresowaniem ze względu na ich właściwości niskotarciowe i przeciwzużyciowe, dużą twardość, odporność korozyjną oraz stabilność termiczną. Celem pracy było przeprowadzenie analizy wpływu topografii powierzchni, z uwzględnieniem jej kierunkowości, powłok diamentopodobnych na właściwości tribologiczne. Oceniano wpływ powłok, ich składu chemicznego, twardości oraz topografii powierzchni na właściwości tribologiczne.
Abstract
The paper presents results of the structure analysis and tribological testing of a-C:H type diamond-like carbon (DLC) coatings produced by the Plasma Assisted Chemical Vapour Deposition (PACVD) technology on 100Cr6 specimens. PACVD methods allow both deposition of thin films on the materials that can conduct an electrical current, and for non-conductive materials, electricity, using a radio frequency discharge currents and low. Essentially, the PACVD process aimed at the production of the hard surface layer or layers having specific properties: e.g. the protective, anticorrosive, tribological. This article discusses the properties of DLC coatings. The surface and cross-sectional microstructure and the chemical composition were assessed by means of a scanning electron microscope (SEM). The structure was studied using a JSM 7100F microscope with an EDS detector manufactured by JEOL. The coatings were analyzed by means of a Talysurf CCI-Lite non-contact 3D profiler. The wear resistance was established under dry friction conditions and in the presence of boundary lubrication conditions with polyalphaolefin PAO-8 oil and was studied by a ball-on-disc T-01M tribometer with the ball being made of 100Cr6 steel and the disc being made of the of 100Cr6 steel coated with DLC. The tribological tests conducted under technically dry friction and lubrication conditions showed that the diamond-like carbon coating had better properties than substrate material. The application of lubricants caused a decrease in the wear of the elements in friction pair. The use of lubricants in combination with a DLC coating has shown that this type of association of the grater greatly affects the smaller friction resistance.
Aneta Jarlaczyńska, Agnieszka Kochmańska, Arkadiusz Woitas
The structure of silicon coatings obtained on TZM molybdenum alloy by slurry method
Struktura warstw krzemkowych otrzymanych na stopie molibdenu TZM metodą zawiesinową
DOI 10.15199/28.2017.5.7
Streszczenie
Celem pracy było wytworzenie krzemowych warstw ochronnych na stopie molibdenu TZM (Titanium Zirconium Molybdenum) oraz charakterystyka ich struktury. Stop TZM jest żarowytrzymały, ma temperaturę topnienia znacznie wyższą niż żelazo, nikiel czy kobalt. Ze względu na zachowanie dobrych właściwości mechanicznych w wysokiej temperaturze jest jednym z najbardziej obiecujących materiałów w energetyce jądrowej, przemyśle kosmicznym oraz lotniczym. W grupie materiałów wysokotemperaturowych stop TZM wykazuje najkorzystniejszą proporcję granicy plastyczności do gęstości. Jednak wykorzystanie jego właściwości jest ograniczone koniecznością eksploatacji w próżni bądź w atmosferze obojętnej (wówczas temperatura pracy tego materiału sięga 1700°C). W środowiskach utleniających w temperaturze powyżej 540°C zarówno czysty molibden, jak i stop TZM tworzą tlenek MoO3, który w temperaturze 790°C ulatnia się, prowadząc do ubytku materiału. Odporność na utlenianie można zapewnić przez wytworzenie w procesie krzemowania na powierzchni stopu warstwy ochronnej składającej się z MoSi2. Podczas utleniania warstwy zawierającej MoSi2 w temperaturze powyżej 1200°C tworzy się na powierzchni tlenek SiO2, który ma charakter ochronny. W pracy przedstawiono wyniki badań opisujące strukturę warstw uzyskanych w wyniku krzemowania stopu molibdenu metodą zawiesinową.
Abstract
Slurry aluminide coatings with newly-developed composition have been produced on Mo-base alloy TZM (Mo - 0.5 Ti - 0.1 Zr - 0.02 C) in an argon atmosphere. The slurry composition was: powder of silicon, halide salts as an activator and a water solution of a soluble glass as an inorganic binder. The coatings were produced at temperatures from 900 to 1200°C and times from 2 to 10 hours. The microstructure, chemical composition using energy-dispersive X-ray spectroscopy (EDS) and phase composition by X-ray diffraction (XRD) of the coatings were determined and the correlation between the technological parameters and the coating thickness was analyzed.
INŻYNIERIA MATERIAŁOWA 4/2017
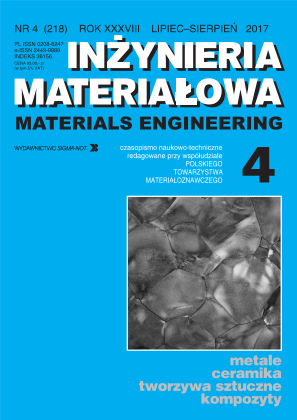
Anna Baran-Sadleja, Janusz Krawczyk, Maciej Motyka, Łukasz Frocisz
Microstructure and hardness of aged Ti-10V-2Fe-3Al near-beta titanium alloy
Mikrostruktura i twardość starzonego stopu tytanu pseudo-beta Ti-10V-2Fe-3Al
DOI 10.15199/28.2017.4.1
Streszczenie
Stopy tytanu pseudo-beta charakteryzują się bardzo dobrą plastycznością oraz małą podatnością na pęknięcia, dlatego przetwarza się je w procesach przeróbki plastycznej. Wykonuje się z nich między innymi odkuwki elementów konstrukcji lotniczych [3]. Analiza danych literaturowych wskazuje na możliwość kształtowania mikrostruktury stopu pseudo-beta Ti-10V-2Fe-3Al w procesach obróbki cieplnej. Wyżarzanie stopu w temperaturze z zakresu dwufazowego α + β umożliwia uzyskanie w mikrostrukturze globularnych wydzieleń fazy α, natomiast nagrzewanie do temperatury wyższej — powyżej temperatury początku przemiany fazowej α + β → β — skutkuje tworzeniem tych wydzieleń w postaci igieł. Objętość względna wydzieleń fazy α zależy od warunków obróbki cieplnej [4]. W pracy podjęto próbę określenia wpływu warunków obróbki cieplnej (starzenia) na mikrostrukturę oraz twardość stopu tytanu Ti-10V-2Fe-3Al. Obserwacje mikrostruktury stopu prowadzono metodami mikroskopii świetlnej i elektronowej skaningowej
Abstract
Microstructural evolution in Ti-10V-2Fe-3Al after specified heat treatment conditions has been the basis of performed analysis. The schedule involves prior heating at the temperature of beta phase occurring, with further aging at the wide range of temperature. Selection of the parameters for heat treatment was carried out on the basis of the calorimetric curve for the investigated alloy. Further research methods were focused on metallographic observations. Hardness measurements were also performed. Conducted researches allowed to determine the aging impact on near-beta Ti-10V-2Fe-3Al titanium alloy properties. Studies revealed that exposure of examined titanium alloy to the relative high temperature (450÷550°C) should be avoided, due to the possibility of ω phase growth. In the other hand presence of hard ω phase is also a grain growth inhibitor, especially while the alloy is heated during long treatment times, ω phase occurrence is also confirmed by the increase in the hardness of samples treated in the temperature range of its occurrence. In order to obtain a two-phase microstructure in analysed titanium alloy, the heat treatment (aging) should be performed at high temperature during long time. Additionally the effects of stress induced martensitic transformation were observed after heat treatment.
Grzegorz Moskal, Damian Migas, Agnieszka Tomaszewska, Tomasz Mikuszewski, Tomasz Maciąg, Marcin Godzierz, Dawid Niemiec
Oxidation performance of Co-Al-W and Co-Ni-Al-W new type of y-y' cobalt-based superalloys
Charakterystyka utleniania nowych nadstopów typu y-y' na bazie kobaltu
DOI 10.15199/28.2017.4.2
Streszczenie
Intensywny rozwój silników lotniczych napędza poszukiwania nowych materiałów żarotrwałych, zdolnych do pracy w coraz trudniejszych warunkach. Efektem tych poszukiwań są nowe nadstopy typu y-y' na bazie kobaltu, charakteryzujące się większą odpornością na utlenianie w wysokiej temperaturze od obecnie stosowanych odpowiedników na bazie niklu. Celem pracy było scharakteryzowanie utleniania nadstopu kobaltu Co-20Ni-7Al-7W w podwyższonej temperaturze i porównanie go z nadstopem bazowym Co-9Al-9W. Praca objęła badania kinetyki utleniania wysokotemperaturowego w warunkach nieizotermicznych metodą grawimetryczną oraz analizę składu chemicznego, fazowego i mikrostruktury powstałej zgorzeliny.
Abstract
Cobalt-based superalloys are class of new heat-resistant materials for components of turbine engines. The y-y' phase microstructure similar to nickel-based analogue, provide excellent creep resistance as well as resistance to corrosion and oxidation. Superior high temperature resistance drives intensive development of Co-based superalloys. The aim of paper is assessment of high temperature oxidation behaviour of Co-9Al-9W and Co-20Ni-7Al-7W alloys in as-cast state. The non-isothermal oxidation performance of Co-9Al-9W and Co-20Ni-7Al-7W alloys was studied using thermogravimetric method up to 1200°C. The thermogravimetric analysis was carried out under argon atmosphere with heating rate 5°C/min. The scale morphology after high temperature oxidation test was investigated. The evaluation of scale concerned macrostructure, microstructure, chemical and phase composition of surface after high temperature oxidation tests. Surface of tested alloys after oxidation was characterized using X-ray diffraction analysis (XRD), scanning electron microscopy (SEM), energy dispersive X-ray spectroscopy (EDS) and light microscopy (LM). Co-20Ni-7Al-7W was characterized by slightly better high temperature oxidation resistance than basic Co-9Al-9W alloy. The surface stability in elevated temperature is important factor in case of components undergoing elevated temperature. This paper shows possibilities of these alloys for high temperature service.
Jerzy Michalski, Hubert Fuks, Sławomir Maksymilian Kaczmarek, Grzegorz Leniec, Barbara Kucharska, Piotr Wach
The magnetic properties of steel after the gas nitriding process
Właściwości magnetyczne stali po procesie azotowania gazowego
DOI 10.15199/28.2017.4.3
Streszczenie
Podczas tworzenia się warstwy azotowanej na stali zmianom ulegają jej właściwości elektryczne (przewodność) oraz magnetyczne, wśród których najbardziej czułe na zmiany fazowe i strukturalne azotowanej stali są względna przenikalność magnetyczna i natężenie pola koercji magnetycznej. W pracy podjęto się zbadania relacji pomiędzy składem chemicznym, rozmiarem i parametrami procesu azotowania stalowych kulek a ich właściwościami magnetycznymi.
Abstract
The paper presents the relationship between the chemical composition of the steel balls, their size and parameters of the nitriding process and magnetic properties defined in the study by EPR and SQUID. The balls made form non-alloyed AISI 1085 and alloyed AISI 420-C steels were investigated. At resonance spectra for both steels before the nitriding process, the resonance signal only existed for two magnetic induction values, 400 mT and 650 mT. This values are untypical because for magnetic centres in the form of iron ions, the expected EPR signal occurs usually in magnetic fields of approx. 340 mT, when the spectrometers operates in the so called microwave X band. This abnormality presumed that the resonance signals did not originate from isolated ions, but instead from magnetically more complex systems, e.g. Fe-Fe pairs or iron clusters, while the observed EPR line position is normally even lower and occurs for a magnetic induction below 200 mT. The fact, that the magnetic centres not had the nature of isolated Fe ions, additionally confirmed the abnormal increase in resonance signal intensity as a function of temperature, which is a behaviour inconsistent with the Curie-Weiss law. After nitriding the AISI 420-C steel in the Nx1021(580/600°C) process, the resonance line became distinctly wider and shifts towards greater magnetic induction values. After nitriding at a lower temperature (the Nx1025(490/520°C process), the resonance lines shifted towards greater magnetic induction values, but, at the same time, the line became more symmetric, closer to the shape of the Lorentz function derivative. The results obtained from measurements by the SQUID method, recording variations in magnetization as a function of temperature, confirm the untypical reinforcement of the magnetic conditions of the samples with the increase in temperature. For the samples tested, the magnetization was relatively weaker, when the tests were conducted in a stronger magnetic field.
Jerzy Michalski, Remigiusz Mruk, Piotr Wach, Kryspin Burdyński
Possibilities of neural networks using in the design, simulation and verification of the controlled gas nitriding process
Możliwości wykorzystania sieci neuronowych w projektowaniu, symulacji i weryfikacji procesów regulowanego azotowania gazowego
DOI 10.15199/28.2017.4.4
Streszczenie
Celem pracy była ocena możliwości wykorzystania sieci neuronowych do projektowania i symulacji kinetyki wzrostu warstw azotowanych na stalli 32CDV13 i 42CrMo4 (40HM), wykorzystując dane uzyskane z modeli analitycznych. W części weryfikacji eksperymentalnej, określenie udarności i odporności na zużycie przez tarcie tych stali po procesie regulowanego azotowania gazowego.
Abstract
The article presents the possibility of neural networks application to design and simulate the growth kinetics of class 1 nitrided layers in steel 32CDV13 and 42CrMo4 (40HM), using data obtained from analytical models. The study analyses unidirectional multilayer neural networks with one hidden layer, with approximation properties. The algorithm developed takes into account the average thickness of the layer of iron nitride. This parameter is most frequently used for the classification of nitrided layers, especially for anticorrosion layers. As a result of research and discussion stated: the neural networks with approximating properties used allowed to build models, well-fitted to the data obtained using analytical models, taught structures of neural networks can be used in systems estimating the results of the nitriding process. The duration of the first stage of the process and the value of the potential in the second degree determine the thickness of the iron nitride layer obtained after the nitriding process. The value of the potential in the second stage also determines the intensity of limiting the thickness of the iron nitride layer. Nitriding decreases the impact strength of steel regardless of the thickness of the subsurface iron nitride layer. The iron nitride layer on the steel increases its resistance to frictional wear. Its resistance to friction wear increases with the increase of the thickness of this layer.
Sebastian Fryska, Jolanta Baranowska
Characterization of mechanical properties of S-phase coatings
Charakterystyka właściwości mechanicznych powłok zbudowanych z fazy S
DOI 10.15199/28.2017.4.5
Streszczenie
Modyfikacja powierzchni stali nierdzewnej o strukturze austenitycznej w celu poprawienia jej właściwości mechanicznych i użytkowych, takich jak twardość czy odporność na ścieranie, jest od wielu lat jednym z głównych zadań stawianych przed inżynierią powierzchni. Jedną z metod poprawy właściwości tych stali jest wytworzenie na ich powierzchni warstwy przesyconego azotem i/lub węglem roztworu stałego austenitu, nazywanego fazą S (także γN lub austenitem ekspandowanym). Jedną z powszechnie wykorzystywanych metod w celu wytworzenia fazy S jest proces niskotemperaturowego azotowania. Warstwy zbudowane z fazy S wykazują większą twardość oraz porównywalną, a czasami lepszą, odporność korozyjną niż stal o strukturze austenitycznej [1÷5]. Proces niskotemperaturowy jest prowadzony w temperaturze poniżej 500°C. W ten sposób zapobiega się powstawaniu azotków (najczęściej azotków chromu), których obecność znacznie zmniejsza odporność korozyjną tych stali.
Abstract
S-phase (γN, expanded austenite) is a metastable nitrogen and/or carbon supersaturated solid solution in austenitic stainless steel. The phase shows comparable or better corrosion resistance and higher hardness as well as wear resistance than austenitic stainless steel. The paper presents results of investigation on mechanical properties of S-phase coatings deposited by reactive magnetron sputtering on austenitic stainless steel substrates. Substrate temperature (200÷400°C) and nitrogen content in reactive atmosphere (15÷50% vol.) were varied. Hardness and Young’s modulus of the coatings were investigated by nanoindentation. Their adhesion was evaluated by scratch test method. Hardness and Young’s modulus depended on nitrogen content in the atmosphere while substrate temperature had a negligible effect. These mechanical parameters depended on the coating microstructure and grain size rather than on nitrogen content in the coating. Results of scratch tests showed a minor effect of deposition parameters on coatings adhesion. It was also observed that for certain parameters of the deposition process a nitrogen diffusion layer in the substrate may form. The presence of the diffusion layer resulted in a decrease of nitrogen content in the coating, but its effect on hardness and adhesion of the coating was not straightforward.
Marta Paczkowska, Łukasz Wojciechowski, Bartosz Firlik, Grzegorz Kinal, Aleksandra Rewolińska
Influence of operation on tram wheels and rails surface layer condition
Wpływ eksploatacji na stan warstwy wierzchniej kół i szyn tramwajowych
DOI 10.15199/28.2017.4.6
Streszczenie
Celem badań było określenie zmian, jakie zaszły w warstwie wierzchniej wybranych kół tramwajowych oraz szyn aglomeracji poznańskiej wynikające z ich eksploatacji. Lepsze zrozumienie zjawisk zachodzących na styku koła z szyną powinno przyczynić się do zwiększenia bezpieczeństwa transportu tramwajowego, a także do zmniejszenia kosztów obsługi.
Abstract
Trams have become a constant in the landscape of many European metropolises in recent decades. The aim of presented research was to evaluate material changes in the surface layer of Siemens Combino, Konstal 105Na, Moderus Beta and Duewag GT tram wheels and rails as a consequence of wheel and rail exploitation in Poznan agglomeration. Microscopic study and hardness measurement were performed. The surface layer of tram wheel was highly deformed, particularly on the top of the wheel flange and under the rolling surface. In the tram wheel so-called overhangs on the top of the wheel flange and on the outer part of the rolling surface were found. Plastic deformation caused an increase of hardness in comparison to the core material. Hardness increase in case of the top of the wheel flange (even 60%) was bigger than in case of the rolling surface (up to 30%). It was also found that the longer approximate total mileage of the wheel was, the higher hardness increase of the surface layer was. ‘White layer’ as a result of presence of higher temperature during exploitation caused by friction was observed. Hard (even 2.5-times harder than the core material) and brittle layer can cause cracks. In case of Moderus Beta and Konstal 105Na wheels in the part from their frontal side decarbonization was noticed. It was stated that decarbonization is also present in the new wheel. It means that it is a defect of PST type wheel production. An area with so low hardness (below 100 HV0.1) could cause faster deformation and wear of whole wheel. A deformation in the surface layer were also revealed in rails. It was observed even in the coating area generated by welding — slip lines in austenite and martensite phase presence. Some recommendations for better wheel exploitation for Poznan Public Transport Company were also determined.
Paweł Tracz, Tadeusz Bacciarelli, Krzysztof Wacławiak, Barbara Kościelniak
Material and technological issues in production of electrostatic precipitators collecting electrodes
Zagadnienia materiałowe i technologiczne produkcji elektrod zbiorczych elektrofiltrów
DOI 10.15199/28.2017.4.7
Streszczenie
Porównano gatunki taśmy stalowej stosowanej do produkcji elektrod zbiorczych w elektrofiltrach suchych, scharakteryzowano proces technologiczny, wskazano tolerancje wykonania elektrod zbiorczych, porównano właściwości mechaniczne poszczególnych gatunków stali. Ponadto pokazano optymalizację procesu profilowania elektrody zbiorczej z zastosowaniem specjalistycznego oprogramowania.
Abstract
Collecting electrodes are the most important components of electrostatic precipitators. Producers of ash removing devices use formed profiles of Sigma type. This topology of electrodes combines the following basic features: high elasticity and rigidity resulting in efficient ash removal; fast dynamic reaction to hitting; limited release, erosion of the ash into the gas because of profile of the electrodes. Collecting electrodes are thin-walled, steel, open profiles. Technological process of electrode manufacturing involves multistage roll forming of steel strip 1.25÷1.5 mm thick, with calibration. Steel grades are chosen for manufacturing according to temperature of operation and composition of industrial gas. Temperature of operation ranges between 150÷300°C. Most producers use DC01 steel grade for collecting electrodes. However properties of DC01 steel grade are not efficient to PN-EN 10130 + A1 regarding cold working. Such criteria are met by grades of DC02 and DC03. In this article the vital structural and material features of steel strips for roll forming process were discussed. Furthermore, the optimization of roll forming process of collecting plate of Sigma type by using dedicated CAD software COPRA RF 2013 has been shown. Numerical simulations lead to comparison between archive data for 13 stages roll forming and current settings for 18-stage one and proved, that today's setting of roll forming reduces displacements by about 70%.
INŻYNIERIA MATERIAŁOWA 3/2017
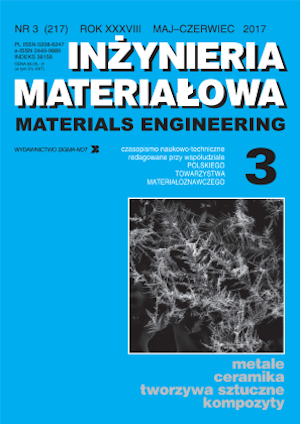
Katarzyna Peta, Piotr Siwak, Karol Grochalski
Research on mechanical properties of aluminum alloys used in automotive industry
Badania właściwości mechanicznych stopów aluminium stosowanych w przemyśle motoryzacyjnym
DOI 10.15199/28.2017.3.1
Abstract
The paper presents one of the most important mechanical properties of aluminium alloys used in the automotive industry, which mainly determine the material resistance to mechanical loads. Samples were made of aluminium alloys from the 3xxx series (core) and 4xxx series (clad). The latter material layer begins to melt at the brazing temperature (582°C) and forms brazed joints between the surfaces of the base sheets. Commonly, these alloys are used as aluminium brazing sheets and applied in automotive to heat exchangers manufacturing, i.e. radiators, condensers, evaporators, heaters, oil coolers and charge air coolers. Samples of these materials were subjected to mechanical property measurements. In order to assess the changes in the materials during their life cycle, the properties after the manufacturing process and the exploitation tests were compared. Therefore, brazing process was realized in N2 controlled atmosphere. Moreover, one of the most important investigations in terms of the heat exchangers working conditions simulation which is resistance to thermal shocks, was performed. The material working conditions indicate that they should comply with above test requirements, including liquid contact, whose temperature range may refer to 0÷90°C. Particular attention was focused on properties such as Martens hardness, Vickers hardness, Young`s modulus and plastic strain, which have significant role in evaluation of product performance and improving its lifetime. For the measurements, a Fischer Picodentor HM 500 nanoindenter equipped with a Vickers indenter was used. The main advantages of the nanoindentation technique are the accurate and reliable results which might optimize heat exchanger. Furthermore, an optical microscopy was applied to analyse the indentations on the sample surfaces.
Jeremiasz Krzysztof Koper, Jarosław Jakubowicz
Cathodic deposition of silver particles on anodized titanium
Osadzanie katodowe cząstek srebra na tytanie utlenionym anodowo
DOI 10.15199/28.2017.3.2
Abstract
The paper presents the process of high voltage anodic oxidation of titanium in the electrolyte containing 2 M H3PO4 + 1% HF. The anodization of titanium was performed at various potentials in the range of 30÷210 V and the time of 30 minutes. As a result, a developed surface titanium oxide on titanium was obtained. Then, on the surfaces of the oxides, silver particles were deposited by cathodic method using the electrolyte containing 0.01 M HNO3 + 0.01 M AgNO3. During the deposition of silver particles, a potential of –1 V was applied for 60 s with respect to the open circuit potential. In order to properly characterize the surface, research techniques were used such as XRD, EDS, SEM as well as corrosion testing. The XRD and EDS examinations have shown the presence of the silver particles on the surface of the titanium oxide. The SEM observations were used to assess the shape and surface morphology of the titanium oxide after anodizing and evaluate the amount of silver particles. The silver particles deposited on the anodized titanium surface exhibited a dendritic shape. On the basis of their arrangement and having monitored the deposition process, it can be assumed that they grow directly from the pores on the oxide surface. This is particularly evident in the most developed oxide surface obtained after oxidation of titanium at 210 V. This research allowed determining the suitability of combined anodic and cathodic treatment of titanium in various electrolytes for medical applications — implants. The resulting morphology of the titanium oxide was evaluated, taking into account the features necessary for the proper osseointegration process (structure, high corrosion resistance and surface morphology). Silver deposited on the anodic oxidized titanium surface causes the oxide layer to exhibit additional bactericidal properties, which is extremely advantageous in medical applications. Excess silver has a negative impact on the surrounding tissue in medical applications. For this reason, the dendritic shape of the obtained particles (high surface area) and their relatively small amount generates a potential in medicine applications.
Tomasz Durejko, Magdalena Łazińska, Cezary Senderowski, Wojciech Napadłek
The FeAl coatings deposited by Laser Engineered Net Shaping
Powłoki funkcjonalne typu FeAl nanoszone techniką laserowego kształtowania przyrostowego LENS
DOI 10.15199/28.2017.3.3
Abstract
The process of manufacturing FeAl coatings by LENS method was presented in this work. The spherical alloy powder of Fe40Al0.05Zr–50 ppm B (at. %) was used as a row material for deposition protective coating on turbine blades. The layered coatings with Ni or 316L zone were also considered. Samples were prepared using LENS 850R system with 1000 W fiber laser and two independently controlled powder feeders. The microscopic examination showed that each technological variants have porosity inherited of porosity of powder particle. A scanning with 700 W of laser beam of deposition area enables substantial elimination of this discontinuities type. The positive effect of this technological solution was also noted for microhardness distribution of samples. The deposited coatings is characterized by 600 HV of microhardness with smooth transition zone between coating/substrate. The strength test (three-point bending) showed the mechanical properties of FeAl samples prepared with LENS are lower by about thirty percent (bending strength, ductility) than the substrate.
Agnieszka Kochmańska, Paweł Kochmański, Michał Kawiak
The structure of aluminide coatings on alloy steels in the area of the welded joints
Struktura warstw aluminidkowych na stali wysokostopowej w obszarze złącza spawanego
DOI 10.15199/28.2017.3.4
Abstract
Preparation of aluminide coatings is used to increase the heat resistance. The coating must be frequently applied to details that were previously welded. The description of the structure of the coating in the area of the welded joint can be important when choosing the proper welding techniques. Butt joints were made using tungsten inert gas, arc welding — the method 141. The main differences between the joints are a kind of parent material and production technology (welding with or without a filler material). Parent materials for making the joins are 1.4749 (X18CrN28) and 1.4404 (X2CrNiMo17–12–2) steels. On prepared samples with joints the silicon-aluminide coating by the slurry method were produced. Samples covered by the slurry were annealed in a furnace with a protective atmosphere of argon at two temperatures 800 and 1000°C for 2 hours. To characterize the structure of the coatings electron microscopy, SEM and EDS X-ray microanalysis were used. It was found that the coatings were formed on the whole test surface. There are strong similarities between the structure of coatings produced in a given temperature despite the use of different substrates and various welded joints. Generally, the coatings produced at a temperature of 800°C are characterized by a three-layer structure, while those at 1000°C have two layers. The thickness of the coating produced at 800°C is from a range of 40 to 65 μm depending on the substrate. The thickness of coatings annealed at 1000°C is in the range of 100 to 200 μm. It is noted that the thickness of the coatings on the parent material is in any case higher than on the weld.
Dariusz Bartkowski, Aneta Bartkowska, Adam Piasecki, Waldemar Matysiak
Microstructure and selected properties of Fe-B coatings reinforced with B4C and Si particles produced by laser cladding using Yb:YAG disk laser
Mikrostruktura i wybrane właściwości warstw powierzchniowych Fe-B wzmacnianych cząstkami B4C i Si wytwarzanych metodą napawania laserowego za pomocą lasera dyskowego Yb: YAG
DOI 10.15199/28.2017.3.5
Abstract
The paper presents the study results of Fe-B coatings produced on C45 steel using laser cladding with powder technology. For this purpose, 5-axis CNC laser machining center equipped with Yb:YAG disk laser with a power rating of 1 kW and three streams powder feeding system. The powder that was used to produce Fe–B coatings was subsequently modified by the particles of boron carbide B4C and Si particles. The resulting powder mixture to the particles included 25 wt % respectively 20% B4C, 5% Si. During these studies a laser beam power of 600 W and variable scanning speed 600 mm/min, 800 mm/min and 1000 mm/min were used. Thickness and microhardness of coatings were investigated and relationship between these properties and microstructure of the applied production parameters were described. The microstructure of producing coatings was characterized by dendritic shape. It was found that boron carbide particles and silicon particles have significant influence on increase the microhardness of produced coatings. Coatings were produced using the prepared powder mixture allowed to obtain more than twice greater microhardness than in case of coatings produced using only the Fe–B powder. Phase composition was examined by XRD. Phases of Fe3B, Fe5Si3, Fe2Si and SiB6 were identified. The influence of B4C and Si particles in the mixture of powder on the corrosion resistance of produced coatings were discussed. It was found gradual reduction of corrosion resistance with decreasing scanning speed of laser beam. Less scanning speed result in less intense interaction of laser beam on the material. As a result of this, the remelting degree of powder material with steel substrate was smaller. The surface condition after corrosion tests were examined using a scanning electron microscope. This paper also shows a calculation related to the power density of the laser beam, interaction time of beam on material and fluence.
Adam Piasecki, Mateusz Kotkowiak, Michał Kulka
Laser boriding of 100CrMnSi6-4 steel using BaF2 self-lubricating addition
Laserowe borowanie stali 100CrMnSi6-4 z zastosowaniem dodatku samosmarującego BaF2
DOI 10.15199/28.2017.3.6
Abstract
100CrMnSi6–4 steel, being a high carbon chromium steel with increased content of manganese and silicon, is commonly used in the bearing industry as a standard material. This material is predominantly applied to elements of rolling bearings taking into consideration its good wearability as well as good resistance to contact fatigue. The diffusion boronizing was a thermochemical treatment which improved tribological properties of this steel. In this study, instead of the diffusion process, the laser boriding was used in order to produce a boride layer on this material. The two-step process was used during laser alloying. First, the surface of the specimen was coated by a paste with alloying material. The alloying material consisted of the mixture of amorphous boron and BaF2 as a self-lubricating addition. Next, the surface was remelted by a laser beam using TRUMPF TLF 2600 Turbo CO2 laser. The microstructure of the layer consisted of the remelted zone with eutectic mixture of iron borides, borocementite and martensite as well as the heat-affected zone with martensite, bainite and retained austenite. The continuous laser-borided layer was obtained at the surface. It was uniform in respect of the thickness because of the high overlapping used during the laser treatment (86%). The hardness decreasing was observed in remelted zone compared to the laser-alloyed layer with boron only. However, the significant increase in wear resistance of laser-borided layer was caused by BaF2 self-lubricating addition. The formation of tribofilm on the worn surface was the reason for improved tribological properties of the self-lubricating layer.
Piotr Dziarski, Michał Kulka, Natalia Makuch, Daria Mikołajczak
Corrosion resistance of laser-borided Inconel 600 alloy
Odporność na korozję borowanego laserowo stopu Inconel 600
DOI 10.15199/28.2017.3.7
Abstract
Inconel 600 alloy is used extensively for a variety of industrial applications involving high temperature and aggressive environments. However, under conditions of appreciable mechanical wear (adhesive or abrasive), this material has to be characterized by suitable wear protection. The diffusion boronizing efficiently improved the tribological properties of this alloy. Nevertheless, the long duration of this process was necessary in order to obtain the layers of the thickness up to about 100 μm. In this study, instead of the diffusion process, the laser alloying with boron was used for producing a boride layer on Inconel 600 alloy. During this process, the external cylindrical surface of base material was coated by paste, including amorphous boron, and remelted by a laser beam. In the remelted zone, the three areas were observed: compact borides zone consisting of nickel and chromium borides (close to the surface), zone of increased percentage of Ni–Cr–Fe matrix (appearing in the greater distance from the surface) and zone of dominant percentage of Ni–Cr–Fe matrix (at the end of the layer). The hardness was comparable to that-obtained in case of diffusion boriding. Simultaneously, the laser-borided layer was significantly thicker. In order to evaluate the corrosion behaviour, the immersion corrosion test in a boiling solution of H2O, H2SO4 and Fe2(SO4)3 was used. As a consequence of selective laser alloying, the difference in electrochemical potentials between the layer and base material caused the accelerated corrosion of the substrate in areas without laser-borided layer. The results showed that laser-borided Inconel 600 alloy could be characterized by the excellent corrosion resistance in such corrosive solution if the whole surface would be covered with laser-alloyed layer
INŻYNIERIA MATERIAŁOWA 2/2017
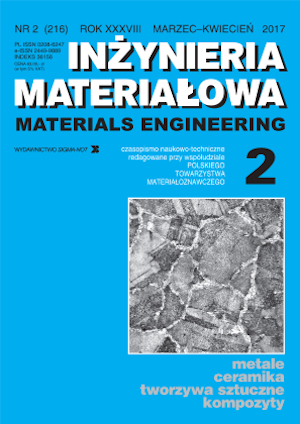
Magdalena Dudek, Bartłomiej Lis, Andrzej Raźniak, Łukasz Zych, Alicja Rapacz-Kmita, Marcin Gajek, Robert P. Socha, Michał Mosiałek, Manuela Reben
Comparative studies of the electrochemical behaviour of Me|Ba0.95Ca0.05Ce0.9Y0.1O3, Me|Ce0.8Gd0.2O1.9, and Me|Zr0.84Y0.16O1.9 systems caused by long-term cathode polarisation, where Me = Ag, Au quasi-point electrodes
DOI 10.15199/28.2017.2.1
Abstract
Electrochemical measurements were performed with applied potential of -0.05 to -0.7 V at 700°C. An increase in absolute current was observed in chronoamperometric curves during long-term negative polarisation from -0.3 to -0.7 V for an Ag quasi-point electrode in Ag|E, E = Ba0.95Ca0.05Ce0.9Y0.1O3; Ce0.8Gd0.2O1.9, or Zr0.84Y0.16O1.9 systems. Decreases in ohmic resistance Rs and polarisation resistance Rp for Ag|Ba0.95Ca0.05Ce0.9Y0.1O3, Ce0.8Gd0.2O1.9, and Zr0.84Y0.16O1.9 systems were determined by means of electrochemical impedance spectroscopy in analogous conditions. Confocal or scanning electron microscopy observation confirmed the migration of silver particles onto ceramic electrolytes under long-term negative polarisation. A silver deposit was found near the site of direct contact of the Ag electrode with the surface of the Ba0.95Ca0.05Ce0.9Y0.1O3 electrolyte. An expansion of the reaction zone in the Ag|Ba0.95Ca0.05Ce0.9Y0.1O3 system is the main reason for the increase in absolute current values. A similar electrochemical response was found in the case of zirconia or ceria-based solid electrolytes with Ag quasi-point electrodes. The effect of the chemical composition and physicochemical properties of ceramic electrolytes and applied negative potential on electrochemical response in Au|Ba0.95Ca0.05Ce0.9Y0.1O3, Au|Ce0.8Gd0.2O1.9, and Au|Zr0.84Y0.16O1.9 systems was recorded. In the case of Au|Ba0.95Ca0.05Ce0.9Y0.1O3 system, during negative polarisation with an applied potential in the range from -0.05 to -0.3 V, a small increase in absolute current values was observed on the chronoamperometric curves. In the case of Au|Ba0.95Ca0.05Ce0.9Y0.1O3 system, decreases in ohmic resistance Rs and polarisation resistance Rp were noticed vs applied potential. Key words: ceramic proton ion conductor, BaCe0.9Y0.1O3, point-electrode, intermediate temperature solid oxide electrolyte, oxygen reduction process.1. INTRODUCTION The [...]
Liwia Sozańska-Jędrasik, Janusz Mazurkiewicz, Wojciech Borek, Leszek A. Dobrzański
Structure and phase composition of newly developed high manganese X98MnAlSiNbTi24-11 steel of TRIPLEX type
Abstract
The work presents the results of investigations of the structure and phase composition of newly developed high manganese X98MnAlSiNbTi24-11 steel of TRIPLEX type. The average density of such steel is 6.67 g/cm3, which is less than for typical structural steels by even 15%. A preliminary analysis of phase composition and structure allows to find an austenitic γ-Fe(Mn, Al, C) structure in the investigated steel with uniformly distributed ferritic α-Fe(Mn, Al) areas elongated towards the boundaries of austenite grains and numerous carbides with differentiated chemical composition and varied size. Nb- and Ti-based complex carbides are dominant in the steel. The investigations of the chemical composition of the carbides revealed in the matrix allow to identify with high probability dispersive κ-(Fe, Mn)3AlC carbides with the nanometric size of approx. 10÷160 nm, which has to be yet confirmed with electron transmission microscopy methods. Fe, Mn and Al as well as small amounts of Nb, Ti and Si are contained in such carbides. The occurrence of aluminium carbonitrides with a fraction of Nb and Ti was also revealed. The size of the above Nb and Ti carbides revealed in solid specimens in the matrix of the studied steel is between approx. 10 nm to 15 μm. X-ray diffraction examinations of carbide isolates prepared by the method of chemical dissolution in HCl showed the existence of NbTiC2 carbides in the studied steel. The diffraction examinations of solid specimens revealed, apart from austenite and ferrite, also the existence of TiC carbides and such initially classified as Mn3.6C0.4 type. Key words: high manganese steels, microstructure, phase composition, NbTiC2, TiC, κ-(Fe, Mn)3AlC.1. INTRODUCTION High manganese steels have become well established in the area of research over high-strength steels which at the same time maintain high plastic properties. Multiple new steel grades containing high contents of manganese (≥[...]
Iwona Bauer
Microstructure and selected properties of chromosiliconized and chromized layers produced on a low-carbon steel
DOI 10.15199/28.2017.2.3
Abstract
The paper presents the results of the microstructure and selected properties examinations of chromosiliconized and chromized layers produced on a low carbon steel. A steel of DC01 grade was designed for the research. The samples were placed in boxes with a special design, containing a pre-prepared powder mixture. The boxes were closed with lids, sealed hermetically using enamel, preventing oxidation of the load and placed in a furnace heated to processes temperature. The microstructure of the analysed layers were evaluated by light and scanning electron microscope. The thickness, surface of samples were determined. Vickers hardness tests were performed on transverse microsections. The phase composition of chromosiliconized and chromized layers was evaluated using a X-Pert diffractometer. Chemical composition was determined by glow discharge optical emission spectroscopy. Chromosiliconized and chromized samples exhibited an increase in hardness and roughness parameters in comparison to the substrate material. Stresses were measured by the sin2ψ X-ray diffraction method. The results of the study show, that chromosiliconizing and chromizing processes generate the state of the compressive internal stresses on the surface of DC01 steel. Key words: chromosiliconizing, chromizing, microstructure.1. INTRODUCTION Various branches of industry are more and more interested in technologies enabling parts of machines and devices to have good functional properties. Therefore, studies on the improvement of methods for the manufacturing of diffusion layers, i.e. gaseous, vacuum, powder, and many other methods [1÷4], are being carried out in many research centres. In the processes of the layers production, the construction of a technological station often incurs a significant financial expense. Thus, in an age of competition, technologies connected with low production costs and good functional properties of the manufactured components enjoy interest.[...]
Karol Dopierała, Janusz Ćwiek, Krzysztof Labisz, Jarosław Konieczny
Application of isothermal heat treatment for perlite rail-steel
DOI 10.15199/28.2017.2.4
Abstract
Rail steel production consists of proper combination of alloying elements and heat treatment, where a wide range of grades can be produced, differing in terms of hardness and the corresponding resistance to wear. A railway’s choice of rail grade is made in terms of traffic and track conditions and excellent service life can be achieved, particularly if modern rail head lubrication and grinding practices are used. This investigations deal with changing the standard heat treatment, based on classic perlitic steel to save energy during the production. For this reason the investigated R350HT steel was subjected to isothermal heat treatment, consisting of hardening to obtain bainitic microstructure. The steel was then annealed, after this step a further cooling took place with furnace then final cooling have been made in air. The microstructure of the steel was examined in the light metallographic microscope Zeiss and scanning electron microscope. In addition, on samples cross-section Vicker's microhardness examination was performed as well as friction wear test was carried out with the use of a tribometer. Also Charpy impact toughness test was performed at room temperature for evaluation of the obtained mechanical properties. On the basis of the carried out analysis of the light microscope structure investigations, it was found, that the microstructure of the R350B steel was formed of relative large irregular grains. The obtained results of the mechanical properties investigations reveals only a low increase of the hardness, wear resistance of the 350B steel compared to the classical 350HT steel. The obtained results have not confirmed the occurrence of the bainitic structure in the 350B steel, however the present ferritic structure reveals some advantage related mainly to lower energy consumption during heat treatment with a hardness and wear resistance values nearly on the same level as in case of the 350HT steel. Key words: isothermal hea[...]
Konrad Cymerman, Andrzej Michalski, Zbigniew Pakieła, Dorota Moszczyńska
Properties of Ni3Al-diamond composites sintered by Pulsed Plasma Sintering
Abstract
This study presents properties of Ni3Al-diamond composites sintered by Pulsed Plasma Sintering (PPS) with the participation of SHS reaction (Self-propagating High-temperature Synthesis). Ni3Al-diamond sinters were produced using Ni:Al (3:1 at.) powder mixtures with addition of 30 vol. % of diamond with grain size ranging from 16 to 60 μm. The sintering process was performed at 1000°C in 5 minutes under load of 100 MPa. Obtained sinters have above 99% theoretical density and show fine crystalline microstructure with relatively uniformed diamond particles, what can be observed in SEM images of polished and fracture surface. The fractures are brittle and have the intergranular character. The X-ray phase examinations have shown that each sinter contains Ni3Al, diamond and Ni3C. The sinters hardness was tested by the Vickers method and oscillated between 580 and 650 HV5. The average grain size of Ni3Al matrix in obtained composites ranged from 2.6 to 3.8 μm. Key words: Ni3Al, Nickel aluminides, diamond, sintering, pulse plasma sintering.1. INTRODUCTION Everyday engineers try to invent and improve existent materials using for cutting tools. Nowadays to machining marble, granite or concrete are using materials with participation of diamond. Adequate wear resistance of the matrix of a diamond tool is the first requirement to attain a satisfactory cutting performance. A wear rate that is too fast will cause premature pullout of the diamond particles, while a wear rate too slow will cause rounding of the sharp edges, commonly known as glazing, and subsequent loss of the cutting capability [1, 2]. The second requirement is good retention of the diamond particles, particularly the protruding ones, which are cutting against the workpiece. Furthermore, the matrix must also have high hot strength and sufficient toughness in order to overcome the high heat and the interrupted vibrations that occur during cutting. Among the various matrix mat[...]
Aneta Bartkowska, Mikołaj Popławski, Grzegorz Kinal, Damian Przestacki
Laser alloying of Vanadis-6 steel by using powders containing boron and tungsten
DOI 10.15199/28.2017.2.6
Abstract
The paper presents the influence of laser alloying on microstructure and microhardness of Vanadis-6 steel. The surface layers were formed by remelting paste which was applied on to the steel substrate. Three kind of pastes were applied: with boron, with tungsten and the mixture of these elements in the ratio 1:1. TRUDIODE 3006 diode laser with nominal power equal to 3 kW integrated with robot arm were used. Parameters of laser alloying were following: power density of laser beam q = 63.69 kW/cm2, scanning rate v = 3.0 m/min and overlap of laser tracks equal to 60%. Microstructure of produced laser tracks were analysed. Surface roughness after laser alloying were investigated. After laser alloying, microstructure consisting with remelted zone and martensitic heat affected zone were obtained. Application of paste with tungsten had contributed to formation the solid solution microstructure, while application of paste with boron or mixture (boron and tungsten) led to formation of boron-martensite eutectic microstructure. Microhardness of laser tracks were measured. It was found that paste containing boron and tungsten allows obtain the layers with increased microhardness compared to steel substrate while maintaining the mild microhardness profile from surface to the substrate. Key words: Vanadis-6, laser alloying, boron, tungsten.1. INTRODUCTION Laser technology is widely used and includes, e.g. the laser alloying [1÷14], laser cladding [1, 2, 15], laser metal deposition [1], laser hardening [1÷3, 16], or laser texturing [1]. Laser alloying involves the simultaneous melting of alloy and substrate material by laser beam, during intense mixing in a weld pool. The alloy material may be applied in the form of paste, tape, powder etc. The laser beam is used to heating of the workpiece surface layer, in order to provide changes in microstructure. It can provide the required mechanical, physical or chemical properties, as well as exploitation proper[...]
Milena Pilarska, Tadeusz Frączek, Katarzyna Ryszko
Short-term ion nitriding process with active screen of technical titanium
Abstract
Studies were carried out on technical titanium Ti99.2 EN10204-3.1 (Grade 2 ASTM) after ion nitriding process in range of temperature between 650°C to 700°C during the time t = 5 h. Process was conducted in nitrogen atmosphere under pressure p = 150 Pa. Samples during nitriding process were put on cathode and additionally they were covered with active screen. Microhardness studies of surface and analysis of obtained surface layer structure allowed to evaluate the role of ion bombardment during the activation of nitride metallic surface. The effect of ion bombardment during the ion nitriding process on the surface of titanium caused to reduce harmful effects of trace amounts of carbon and oxygen impurities. Processes performed at temperature below 700°C did not allow to produce an uniform zone nitride on the surface subjected to the gas nitriding. It has been shown that nitriding processes carried out at 650°C and 675°C result in the formation of homogeneous nitrided layers only on the surface subjected to plasma effects. The surface layers created by gas nitriding are characterized by a lower microhardness of the surface. It was found that the increase of the process temperature to 700°C resulted in the formation of nitride layers with comparable properties on both surfaces of the sample, as confirmed by measurements of surface microhardness. It has been found nearly 2.5-fold increase in the surface microhardness variant adopted for the ion nitriding at 700°C for material in the initial state. Key words: ion nitriding, active screen, titanium.1. INTRODUCTION Titanium and titanium alloys have some very attractive properties which allow them to be used in many industries. Some of their advantages are: excellent corrosion and erosion resistance, low densities which give them high strenght-to-weight ratios allowing to obtain stronger structures, high-temperature capability and in some cases cryogenic properties [1]. They are widely used in aeros[...]
Aleksandra Szram, Jerzy Sokołowsk, iJoanna Nowak, Monika Domarecka, Monika Łukomska-Szymańska
Mechanical properties of composite material modified with essential oil
DOI 10.15199/28.2017.2.8
Abstract
Recurrent caries is an omnipresent problem in dental practice. More than half of all restorations need replacement in 10 years time. Upon tooth preparation, dentine is more susceptible to microorganism colonization. Hence antibacterial properties in novel composite materials are crucial issue. Such substances as essential oils may set an alternative compound for antibacterial compounds used in materials available on the market. Essential oils are concentrated hydrophobic liquids, that contain volatile aroma compounds. These compounds, especially terpenes, present antibacterial activity to caries-related microorganisms. The antibacterial effectiveness of several essential oils has been already scientifically proven. For instance, cinnamon oil thanks to its properties is often used in medicine. The essential oil derived from its bark consists of trans-cinnamaldehyde which has antimicrobial effects against plant pathogens, food poisoning, fungi and spoilage bacteria. The aim of the study was to evaluate mechanical properties of commercial composite, modified with essential oil. In the study SDR composite (Dentsply) was modified by adding cinnamon essential oil (Dr Beta, Poland). The material of 2 g was mixed with 1 μl, 2 μl and 5 μl of cinammon oil until homogenous structure was obtained (group I, II and III). Control sample group comprised specimens of SDR material without modification. Mechanical properties were tested by diametral tensile strength test, three-point bending test and Vicker’s hardness. Results showed that modified material gained lower mean values in DTS and HV1 tests for all groups in comparison to control sample group. However, mean TPF values for group I were higher when compared to control sample group. Mechanical properties of experimental material may be accepted from clinical point of view when used as temporary fillings for instance in paedodontics. Key words: essential oil, diametrial tensile streng[...]
Adrian Krzysztof Antosik, Zbigniew Czech
Preparation of mounting mass
Abstract
Self-adhesives materials are materials that develop significant adhesive forces upon contact with a substrate without requiring a chemical reaction without leaving residues on the substrate. To exhibit this property, self-adhesives materials should have cohesive strength that is much higher than its adhesion strength to the substrate. Usually they are defined as a viscoelastic material, which in a solvent free state remains permanently tacky at room temperature. Mechanically, they are a soft, sticky substance; consequently, a supporting backing is often required to convert it into commercially useful forms, such as tapes and labels. Mounting mass are a special form of self-adhesives materials usually in similar to modelling clay form plasticizer after warming up in the fingers. They are characterized by the fact that it does not dry out and can be relatively easily peeled off. They are used, inter alia, for fastening light units (including posters) to dry surfaces (walls, tables). The first company producing them was the company Bostik, the product Blu-tray, the composition of which is the secret of the manufacturer, generally described as a mixture of synthetic rubber, not showing dangerous properties in normal applications. Currently it is known a lot of self-adhesive products in the form of plastic masses produced by industry names “Blu-Tac" (Bostik), “UHU tac patafix" (Uhu GmbH) or “Prott buddies" (Henkel). Preparation of novel mounting mass using composition silicone risen with trimethylopropane triacrylate crosslinking by the use of UV or LED radiation was presented. Their adhesive properties on various substrates and cohesiveness are determined using international standards. Obtained materials are characterized by excellent cohesion and enough adhesion. Key words: mounting mass, silicone resin, UV-crosslinking, LED-crosslinking.1. INTRODUCTION In principle, if the work required separating two dissimilar objects is hig[...]
INŻYNIERIA MATERIAŁOWA 1/2017

Anna Matras, Agata Roguska, Małgorzata Lewandowska
Fabrication of nanotubular oxide layer on Ti-24Nb-4Zr-8Sn alloy by electrochemical anodization
DOI 10.15199/28.2017.1.1
Abstract
Nanotubular oxide layer of TiO2 was fabricated by electrochemical anodization of Ti-24Nb-4Zr-8Sn alloy in electrolyte containing water, glycerin and ammonium fluoride. Physicochemical characterization was performed in order to evaluate the structural and chemical properties of obtained layer. Variable parameters such as voltage (10 V, 20 V and 30 V) and anodization time (10 min and 40 min) were applied to determine the influence of those factors on the morphology and chemistry of fabricated titania nanotubes. Scanning electron microscopy was used to assay the architecture of obtained nanotubular layer and the impact of anodization parameters on the produced structure. Chemical and structural analysis were conducted by energy dispersive X-ray spectroscopy coupled with scanning electron microscope and X-rays diffraction technique. Obtained results allowed to declare that morphology of the nanotubes depends on voltage applied and duration of the anodization. For higher voltage applied, the nanotubes with bigger diameter are obtained. For layers fabricated at 10 and 20 V, increase in anodization time results in obtaining more homogeneous oxide structure (the diameter distribution is narrow) as well as decrease of characteristic dimensions values (wall thickness and diameter). For structures anodized with 10 V, the average nanotubes diameter was 38 nm while for layer fabricated with 30 V, the average diameter was 101 nm. The most uniform nanotubular structure was fabricated by anodization at 20 V for 40 min. Chemical analysis revealed presence of such elements as titanium, oxygen, niobium and tin. However, thickness of the nanotubular oxide layer is about hundreds of nm, therefore additional examination need to be done to determine whether the nanotubes contains alloying elements (Nb or Sn) or the signal comes from the substrate. In general, the chemical composition of the anodized nanotubes corresponds to the composition of the substrate Ti2448 all[...]
Sławomir Kotowski, Andrzej Nowotnik, Jan Sieniawski, Andrzej Butkiewicz
The application of tumble finishing in surface preparation process for deposition of TBC coatings
DOI 10.15199/28.2017.1.2
Abstract
Thermal barrier coatings (TBC) are widely used for protection of turbine blades against aggressive thermomechanical and chemical degradation during operation in hot section of aircraft engine. Quality and properties of TBC coating is strictly related to preparation of substrate material (grinding, and rounding off edges, polishing and cleaning). In the article, tumble finishing as method for surface preparation before deposition of thermal barrier coatings has been described. The process was performed for different types of ceramic feedstock and base material in order to obtain homogeneous roughness. Tumbling was carried out using centrifugal polishing machine. The research was divided into three stages. The first one consisted in investigation of the influence of rotational velocity and water flow, on the course of tumbling process. Afterwards, proper type of ceramic feedstock has been selected. During the last stage, ready-to-use recipes for polishing of samples made of for CMSX-4, Inconel® 718 and stainless steel 1.4016 were developed. Key words: tumbling, tumble finishing, TBC, thermal barrier coatings, surface preparation.1. INTRODUCTION Taking into account the actual trends in aircraft engine design, including constant shifting conditions in the hottest section of aircraft engines towards higher temperature and more aggressive thermomechanical and chemical conditions, it is imperative to apply materials characterized by highest mechanical properties and protective coatings providing thermal insulation and chemical barrier for base material. Increasing the operating temperature allows to improve the engine efficiently and reduce fuel consumption and the emission of carbon dioxide [1, 2]. This canalizes the research on modification of engine design in order to improve the resistance to influence of high temperature, oxidizing gases environment and mechanical loads which are present in operating conditions. In the article, the c[...]
Robert Albrecht, Włodzimierz Bogdanowicz, Kamil Gancarczyk, Jan Rak, Jan Sieniawski, Krzysztof Kubiak, Józef Lelątko
Microstructural characterization of creep in the single crystal superalloy CMSX-4
DOI 10.15199/28.2017.1.3
Abstract
Blades and vanes structural components of turbine engines are processed to withstand high temperature during loading conditions of service, fulfilling high standards of quality control and safety for effective use. Therefore, characterization of mechanical properties, such as creep behaviour, are necessary for appropriate control procedures on prediction of exploitation lifetime. The materials mostly used in manufacturing of these components are single crystal nickel-base superalloys. Creep behaviour characterization, composed of creep-rupture tests, were performed on a single crystal rods made of CMSX-4 superalloy obtained at a withdrawal rate of 3 and 5 mm/min. Cylindrical rods were directly solidified in the [001] direction in an ALD Vacuum Technologies investment casting furnace (VIM-IC 2). Then, prepared specimens were tested in tensile creep under constant stress of 248 MPa at a temperature of 982°C. The longitudinal and cross sections from tested samples, were characterized by TEM and X-ray diffraction methods. It was found that all samples showed a similar rupture mechanism. The electron backscatter diffraction (EBSD) measurements showed that octahedral and cubic slip systems were present however, the critical stress was present on {111} planes. It was observed that the cubic slip has the highest calculated Schmid factor along the dendrite cores while the octahedral slip occurs through entire sample volume. Samples obtained at 5 mm/min possess a visible widening of coherent scattering regions as shown in inverse pole figures. The reason of these changes is the fact that higher rate has the greatest probability of creating small angle boundaries, often occurring in the interdendritic channels. Key words: CMSX-4, single crystal, superalloy, creep.1. INTRODUCTION Single crystal superalloys are widely used in the hot section of gas turbines due to their excellent resistant for creep, fatigue and oxidation at high temperature [1]. They ar[...]
Janusz Krawczyk, Adam Kokosza, Jerzy Pacyna, Marcin Madej
Tribological and material utility aspects of mill rolls for cold rolling
DOI 10.15199/28.2017.1.4
Abstract
In the present work, quantitative and qualitative indicators related to wear have been proposed based on the results of the research conducted on damaged mill rolls working in a modernized rolling mill, as well as the technical data related to rolling. It has been found that previously used mill rolls were worn by two main mechanisms, i.e. abrasive wear and fatigue wear. The fatigue mechanism is the main reason for the rolls being removed from further exploitation. Tribological laboratory tests were performed by means of the T05 tester (a block/ring wear testing system) with the load of 100 and 300 N applied for 2000 s. The 100Cr6 bearing steel with the hardness of 57 HRC was applied as the counter-sample. The X153CrMo12 and 70MnCrMo8-2 steels were used as the research material. The tempering temperature of 100 and 150°C were used for the X153CrMo12 steel and 100°C for 70MnCrMo8-2 steel. It has been shown that the steel characterized in a microstructure composed of primary carbides (X153CrMo12 and previously used material). The role of the primary and secondary carbide precipitations as abrasive particles has been indicated in the work. It has also been proven that increasing the tempering temperature results in an increased wear of the 70MnCrMo8-2 steel. The conducted research allows for a proper selection of the tempering temperature (100°C). This confirms the assumed concept of the proposed roll heat treatment. A verification (monitoring) of the working rolls’ wear was based on the observations of the cracks formed during their usage and the roughness measurements carried out at three locations across the width of the strip. Key words: cold rolling, mill rolls, tribology, tool steel, primary carbides.1. INTRODUCTION Mill rolls working in cold rolling mills wear mainly because of two mechanisms: abrasive wear and fatigue wear. This results from the stresses present during the rolling process [1, 2]. An intensive abrasive wear blocks [...]
Adrian Mróz, Dariusz Garbiec, Jarosław Jakubowicz, Łukasz Łapaj
Effect of manufacturing technology of ball-and-socket joint made of Co28Cr6Mo alloy on its tribological properties
DOI 10.15199/28.2017.1.5
Abstract
The article presents the results of friction and wear testing of ball-and-socket joints, made of ASTM F75 alloy powder, applying the technologies of selective laser melting and spark plasma sintering. The reference material constituted joints produced by machining from a ASTM F1537 LC rod. The tribological tests were carried out using the movement simulator of a spinal motion segment of our own design, in the environment of distilled water. The test results consisted of a comparison of the friction resistance values occurring in the friction couple and comparison of the wear indicators of the upper and lower components, which simulate the tribological system of an intervertebral disc endoprosthesis in the spinal lumbar segment. Analysis of the wear mechanism of the bearing surfaces was performed on the basis of microscopic observations and measurements of friction surface roughness. Regardless of the manufacturing technology, the coefficient of friction varied in the range of 0.25 to 0.30, wherein a median value for all the tested material combinations was in the range of 0.27 to 0.29. The lowest resistance to tribological wear was demonstrated by the joints produced employing spark plasma sintering technology. The wear of the joints produced with this technology was about 20% higher in comparison to those joints formed by selective laser melting, and about 30% higher compared to the joints produced in a conventional manner from ASTM F1537 LC alloy. Observations performed using scanning electron microscopy showed that regardless of the production technology, the dominant type of wear was abrasive-adhesive wear. Unlike the joints produced in a conventional manner, the bearing surfaces of the components produced by means of selective laser melting and spark plasma sintering technologies, there is evidence of fatigue damage. The results call into question the possibility of using alternative technologies in the manufacturing process of endoprosthe[...]
Łukasz Wzorek, Mateusz Wędrychowicz, Tomasz Skrzekut, Piotr Noga, Marcel Wiewióra, Jakub Wiewióra, Wojciech Sajdak, Maria Richert
Effect of heat treatment on quality and properties of solid bonded 6061 aluminum alloy
DOI 10.15199/28.2017.1.6
Abstract
In these studies, the effect of heat treatment on solid bonded AA6061 aluminium alloy has been investigated. The examined material in the form of powder and rapidly solidified ribbons was subjected to pre-compacting and extrusion carried out at elevated temperature. As a reference material, a billet from the solid AA6061 alloy was subjected to the same procedure. Samples of obtained profiles were subjected to the subsequent heat treatment operation. Surface quality and mechanical properties of materials before and after annealing were compared. The increase in mechanical properties was accompanied by a well visible post-heat treatment blistering effect. Key words: heat treatment, solid bonding, aluminium alloy.1. INTRODUCTION High popularity of Al-Mg-Si alloys in the extrusion industry is mainly derived from their unique properties such as high specific strength, good corrosion resistance, and excellent formability. Furthermore, the heat treatability of these alloys allows improving their mechanical properties though at the cost of ductility [1, 2]. Technical literature provides rich information on the kinetics of Al-Mg-Si precipitation strengthening [3÷7]. According to [8], the precipitation sequence can be divided into the following stages: Al SSS → clusters of Si/Mg → GP zones → β″ → (βʹ + U2 + U1 + Bʹ) → β In the early phase of heat treatment, “clustering" of Si and Mg atoms occurs inside the saturated solid solution (Al SSS) and is followed by subsequent dissolution of Mg clusters and formation of Mg/Si co-clusters. These structural changes lead to exothermic effects and changes in electrical properties [4]. GP zones are the first important metallic phase that arises during precipitation strengthening and is stabilized by high silicon content [9]. The major hardening effect in Al-Mg-Si alloys is attributed to the presence of the needle-shaped β″ phase[...]
Katarzyna Piwowar, Janusz Trojanowski, Anna Drobek, Tomasz Malinowski, Grzegorz Mońka, Tadeusz Wierzchoń
Modelling of the structure and mechanical properties of 32CDV13 steel under glow-discharge nitriding for the industrial technology application
DOI 10.15199/28.2017.1.7
Abstract
The manufacturing of surface layers are increasingly used in industry, as the effective method of improving the useful properties of the machine parts. The specific properties of the nitrided layers such as low temperature of process may be an alternative to the commonly used technology like high-temperature carburizing or carbonitriding in the aerospace industry. The article presents the results obtained after nitriding of complex samples made with 32CDV13 steel. As our research improves the properties of surfaces can be controlled by the process parameters as temperature, duration time, composition of the reactive atmosphere, the pressure (vacuum) and the activation of the surface by cathode sputtering process in the initial stage of the treatment. Key words: glow-discharge nitriding, surface layer, structure, phase composition, residual stresses, corrosion and wear resistance, fatigue strength.1. INTRODUCTION The manufacturing technology of diffusion surface layers under glow-discharge conditions on the cathode potential and their modification in the plasma region are increasingly used in industrial technology as an effective method of improving the production of machine parts at a lower cost of manufacturing. Some specific properties of nitrided layers such as: low temperature of process, high value of hardness, wear resistance and fatigue strength can be an alternative to the commonly used high-temperature carburizing or carbonitriding in the aerospace industry. The paper presents the characteristic of structure and mechanical properties of the layers produced under glow-discharge nitriding on cathode potential related to the basic process parameters. Furthermore the results show that the all presented properties of the 32CDV13 steel can be controlled by the process parameters as temperature, duration time, composition of the reactive atmosphere, the pressure (vacuum) and the activation of the surface by cathode sputtering proces[...]
Kinga Bociong, Dorota Rylska, Jerzy Sokołowski
The modification of dental resin composite using selected dimethacrylate monomers
DOI 10.15199/28.2017.1.8
Abstract
The use of dimethacrylate resin composite in dentistry involves the potential of shrinkage and then stress contraction. This leads in consequence to defects and even secondary caries. The aim of this study was to modify the commercial resin-based composite using selected monomers and to assess the influence of such additives on polymerization stress and bulk mechanical properties. The polymer matrix was modify due to implementation monomers with differentiated chemical constitution. Stresses generated by the filling were calculated on the basis of the theory of elasticity patterns. The depth of cure and microhardness was evaluated as well. On the basis of measurements, it has been found that stress could be reduced even up to a half when composite is chemical modified by adding not less than 0.25 wt % of 1,6-hexanediol dimethacrylate or diurethane dimethacrylate. Key words: dimethacrylate resins, dental composites, stress contraction, chemical modification.1. INTRODUCTION Cuspal fracture and recurrent caries continually are directly causes of failure of resin composite restorations [1÷3]. During solidification of resin composites stress develops at the restoration-tooth interface. The major cause of it is polymerization contraction of both methacrylate filling and the adhesive agent [4, 5]. Other consequences of the contraction stress are extensively reported in the literature [6, 7]. The elimination or significantly reduction of shrinkage during the polymerization processes is one of the major problem in the development of dental composites. Many factors influence contraction stress in dental composites. These can be divided into material formulation factors, eg. monomer structure and chemistry, filler type and amount, filler-polymer matrix interactions etc. [5]. Secondary group of factors are those connected with material polymerization factors, such as polymerization initiators, inhibitors, cavity geometry, curing method, placement [...]
Sebastian Stanisławek, Piotr Kędzierski, Danuta Miedzińska
Comparative fracturing of marble samples with fluids of different viscosity
DOI 10.15199/28.2017.1.9
Abstract
This paper presents an experimental study of rock samples fracturing with pressure from fluids of different viscosity. Fracturing pressure is one of the most important factors influencing effectiveness of a well-stimulation. It influences both the design of the pressure installation and seismic activity of the area. Authors analysed how fluid viscosity influences material resistance to pressure. As the rock type, marble was chosen. Three fracturing fluids were tested: water (20°C), supercritical carbon dioxide (42°C, 10 MPa) and hydraulic oil H46. The obtained results indicate that fracturing fluid viscosity is an important factor influencing the pressure level required to initiate and propagate fractures. The lowest pressure was detected for carbon dioxide (10.0 MPa). For water test pressure was 16.2 MPa while for oil, which has the highest viscosity, it reached 19.2 MPa. Moreover depending on the fluid type, sample damage could be observed in different planes. Key words: fracturing test stand, hydraulic fracturing, rock tensile strength.1. INTRODUCTION Hydraulic fracturing is useful in geotechnical and mining applications [1]. However, the details of fractures initiation and propagation are difficult to foresee. Nowadays, well stimulation is one of the most promising techniques of increasing the yields of wells that produce oil, natural gas, water or steam. Fracturing pressure is one of the most important factors influencing effectiveness of the process. It influences both the design of the pressure installation and seismic activity of the area. Unfortunately, induced seismicity and water contamination cause environmental concerns associated with large scale hydraulic fracturing. It resulted in political efforts to ban legally the technique in many countries around the world. Therefore, application of the lowest fracturing pressure, which is required for proper well stimulation, is very important. The pressure depends on many factors[...]